This
technique is seldom used with braille scale models, but once you start
superdetailing or scratchbuilding models, it certainly can have it
uses.
Soldering
is an excellent way of obtaining strong joints between metal parts,
especially those connections that are impossible to achieve (or could
never be as strong) with glue. However, there are a numbers of disadvantages,
the biggest of them being the fact that it must be done before the
metal parts are glued onto the plastic model (which would inevitable
melt!), which makes good planning necessary. |
Here
you see a number of examples, some parts which I made using solder
and heat, in scales ranging from 1/35 to 1/72. |
 |
As an
example, I'll make a construction using some thin copper or brass
wire. This is available in several thickness; for Braille models,
I mostly use all sizes between 0,2 en 1 mm |
 |
These
wires are invariable sold in coiled form.
To make it easier to straighten them, is it imperative to heat the
wire above a flame until it's glowing red and then submerge it immediately
in some cold water. This technique takes away the stiffness out of
the metal, making it easier to bend or straighten. Once your piece
of wire has cooled down, put it on a cutting mat and, using soft pressure,
drag a steel ruler over it back and forth until it is completely straight. |
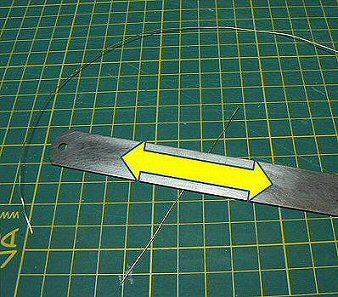 |
What
do you need next, besides a good soldering iron (I use a simple
30 Watt iron with a sharp point) ?
|
|
Some
soldering tin, "flux" acid paste (available as solder
fat or liquid) and Pritt Multi Fix (which is a European variant
of Blue Tack).
|
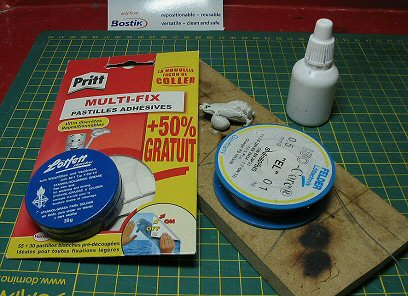 |
DIY
shops sell different types of soldering tin, ...
|
 |
...
but I always look for the finest wire available (my favorite is
0.5mm thick, composed of a 60%tin/40%lead alloy).
|
 |
You
also need a small wooden block, a couple of toothpicks and clothespins
to protect hands and table against the heat. I adapt the ends of the
clothespins by cutting of some wood to obtain a better grip.
Most soldering is done in two dimensions, however, should I have to
make a three dimensional connection using some wooden profiles glued
on my wooden block can make it easier to hold the lose pieces in place.
|
 |
To
demonstrate my method, I'll solder a vehicle light support, connecting
three wires into a letter "H" Before starting, a word of
caution, a soldering iron is hot (200 to 300° C, 400 to 570°
F), so use it wisely!
The first
tip I'd like to share with you : if possible, always cut your brass
or copper wire longer than needed! This makes it easier to emplace
the (often very small) pieces in the correct angle or position before
adding the solder, making your end product much better. |
If
feasible, you should always "pre-tin" your wire by melting
a thin coat of tin on the connecting points. This will make the soldered
joint stronger. How to proceed? First, put a bit of flux on your wire,
... |
 |
... then
bring the wire in contact with the solder. Next, let the preheated
iron touch the wire, as closely to the solder, but not into it.
|
 |
The
soldering iron should heat the wire until the latter reaches the melting
temperature to make the tin flow and fix itself onto the greased wire.
A mistake commonly made is to touch the tin with the iron,
thereby melting the tin but without the wire having the desired temperature
which will result in a weaker joint.
Remember
: liquid tin has a beautiful shine, cold tin is matt.
As soon
as the wire has a nice coat of tin, gently remove the iron from it,
which will make the tin turn matt. Repeat this with the other wires,
the result should look like this : |
 |
Once
all the wires properly tinned, we can proceed with the next step.
Using the Blue Tack, both wires are immobilized in the correct position
on the wooden block. |
 |
Apply
a bit of flux where the joint should come. Once again, let the soldering
iron touch one to the wires as close as possible to the fat (but not
in it); After a few seconds, the tin present on both wires will become
liquid and merge on the greased connection. Taking away the iron will
harden the solder.
Check the result and if satisfying, carefully start removing the Blue
Tack. Should this putty be difficult to remove, by gently pressing
another small ball of Blue Tack onto it, the remaining stuff should
come loose. Always try to avoid exercising strong pressure on the
joint, e.g. when filing away some surplus solder.
|
 |
Now
we can start connecting the third wire. Cut the perpendicular wire
to the desired length. Pre-tinning the remaining short end is impossible,
because the heat could also dissolve the connection we’d just
made. The new wire however will get this treatment.
Once again, immobilise everything in the desired position on the wooden
block using Blue Tack. Also put a bit of putty on the previously connection
made; this will drain some heat away from these wires, preventing
that connection to come loose.
However,
make sure your iron will have free access to the third wire.
|
 |
Next,
follow the same procedure : apply grease to the new joint and let
the iron shortly touch the third wire until the tin connects with
the short wire.
Remove
the soldering bolt and inspect the result. If OK, remove the surplus
tin with a metal file or abrasive paper. Take care not to remove the
tin in the joint itself, otherwise you’ll have to start all
over again.
Once
the clean-up terminated, you can cut every wire to the correct length. |
 |
This
image shows the work piece installed on the model, waiting for its
light to be added...
|
 |
...
and then with the plastic light glued onto it.
|
 |
Another
example of the soldering technique to get stronger mudguards
|
 |
One
final tip, soldering goes relatively fast once your iron is hot, so
why not make a couple of work pieces more than needed? Then you can
choose the best one and thus get a better model.
Happy
soldering…
|
 |